Le processus de production des granulats
La production des granulats se déroule suivant cinq étapes principales : le décapage des niveaux non exploitables, l’extraction, le transfert sur les lieux de traitement, le traitement des granulats pour obtenir des produits finis, le stockage et la livraison.
Le réaménagement du site se fait quant à lui de façon progressive, tout au long de l’exploitation. Les techniques d’exploitation dépendent du type de site d’extraction de granulat :
- Les carrières en milieu sec ou en site immergé de roches meubles (gisements de sables et graviers), Les carrières de roches massives (gisements de roches dures).
- Les extractions marines
Les extractions marines
Les granulats marins font partie des sédiments meubles garnissant le plateau continental. Ce dernier constitue la partie du fond de la mer qui s’étend avec une pente modérée entre le littoral et le talus continental (Manche et Océan Atlantique).
En ce qui concerne les techniques d’exploitation des granulats marins, il en existe deux sortes :
- Les dragues à bennes preneuses
- Les dragues aspiratrices
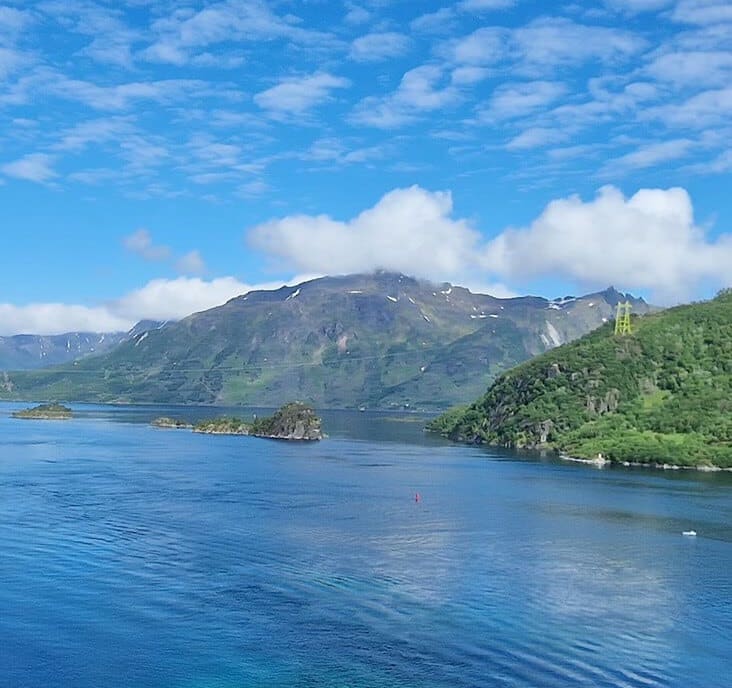
L’extraction à l’aide de dragues à bennes preneuses est encore très répandue en France par leur nombre mais non par les tonnages correspondants. Les entreprises s’orientent de plus en plus vers les dragages aspiratrices en marche pouvant décharger par refoulement hydraulique.
L’extraction des granulats marins par drague aspiratrice est réalisée par des navires équipés d’un système d’aspiration en marche qui quadrillent le site d’extraction à vitesse réduite. Ces navires ont la particularité de réaliser à la fois les travaux d’extraction, le transport et le déchargement des matériaux sur des installations industrielles et portuaires adaptées.
Le déchargement des matériaux se déroule sur des sites terrestres. Selon leurs caractéristiques, les matériaux font l’objet d’un traitement (concassage, criblage, lavage éventuel) pour répondre aux spécificités des demandes.
Une fois traités, ils sont acheminés jusqu’aux lieux de consommation, par route ou voie d’eau.
Les granulats marins lorsqu’ils sont pratiquement exempts de sel (tels que ceux extraits et déchargés par pompage hydraulique) présentent des caractéristiques comparables à celles des granulats alluvionnaires (roches meubles), mis à part leur manque de fines qu’il faudra corriger par apport de fines d’ajout, en particulier pour les usages dans les bétons et mortiers.
Recyclage des eaux de lavage
Dans le cadre de leur activité de production de granulats, les exploitants de carrière ont pour obligations de ne pas rejeter les eaux de lavage chargées en fines particules minérales à l’extérieur du site, et de les recycler intégralement. La décantation naturelle est le procédé le plus couramment mis en œuvre pour respecter les termes de cette réglementation. Cette technique consiste à rejeter les eaux chargées dans des bassins où les fines vont sédimenter ; l’eau clarifiée est pompée à l’aval du bassin et recyclée dans l’installation.
Le circuit de recyclage doit être conçu de telle manière qu’il ne puisse donner lieu à des pollutions accidentelles. Un dispositif d’arrêt d’alimentation en eau de procédé de l’installation, en cas de rejet accidentel de ces eaux, est prévu.
Outre la décantation naturelle, d’autres techniques peuvent être mises en œuvre :
- La floculation est un processus d’agrégation des fines par des macromolécules organiques appelées floculants ;
- La décantation en décanteur/clarificateur permet de recycler en ligne jusqu’à 90% des besoins en eau de procédé et ainsi de réduire la charge d’eau circulante de l’installation ;
- Le filtre-presse, qui s’utilise en complément d’un décanteur/clarificateur, permet d’obtenir des rejets pelletables et de s’affranchir des bassins de décantation.
Contrôle qualité
Comme tous les produits entrant dans la constitution d’ouvrages à hautes performances, les granulats doivent répondre à des critères de qualité qui dépendent, d’une part, de la nature de la roche (résistance aux chocs et à l’usure, caractéristiques physico-chimiques, …) et d’autre part, de caractéristiques liées à leur élaboration (dimension, forme, propreté, …)
Créée dès 1992 à l’initiative de l’UNPG, l’Association technique pour la certification des granulats (ATCG) gère la marque NF Granulats sous l’égide de l’AFNOR.
La certification nécessite de mettre en œuvre, dans chaque site de production de granulats, un système de contrôle de la qualité tout au long de l’élaboration des granulats. Conformément à des normes d’essais et des normes produits, ce contrôle comporte, entre autres, des tests sur le produit fini : dureté, propreté, granulométrie, … La mise en place d’un système de qualité permet de s’assurer de la conformité aux normes de la totalité de la production, et pas seulement du lot contrôlé.
Stockage et livraison
En fin de traitement, on obtient des produits de qualités qui répondent à des critères de qualité bien précis.
L’exploitant peut aussi réaliser des mélanges avec des proportions précises pour chaque composant, ceci en vue d’utilisations particulières ou pour économiser les gisements.
Une fois réduits, traités et classés, les granulats sont acheminés vers les aires de stockage, soit sous forme de tas individualisés, soit en trémies ou silos.
Leur acheminement jusqu’au client peut se faire par camion, par train ou par péniche.
Le client peut également faire enlever les matériaux directement sur le site par camions-bennes.
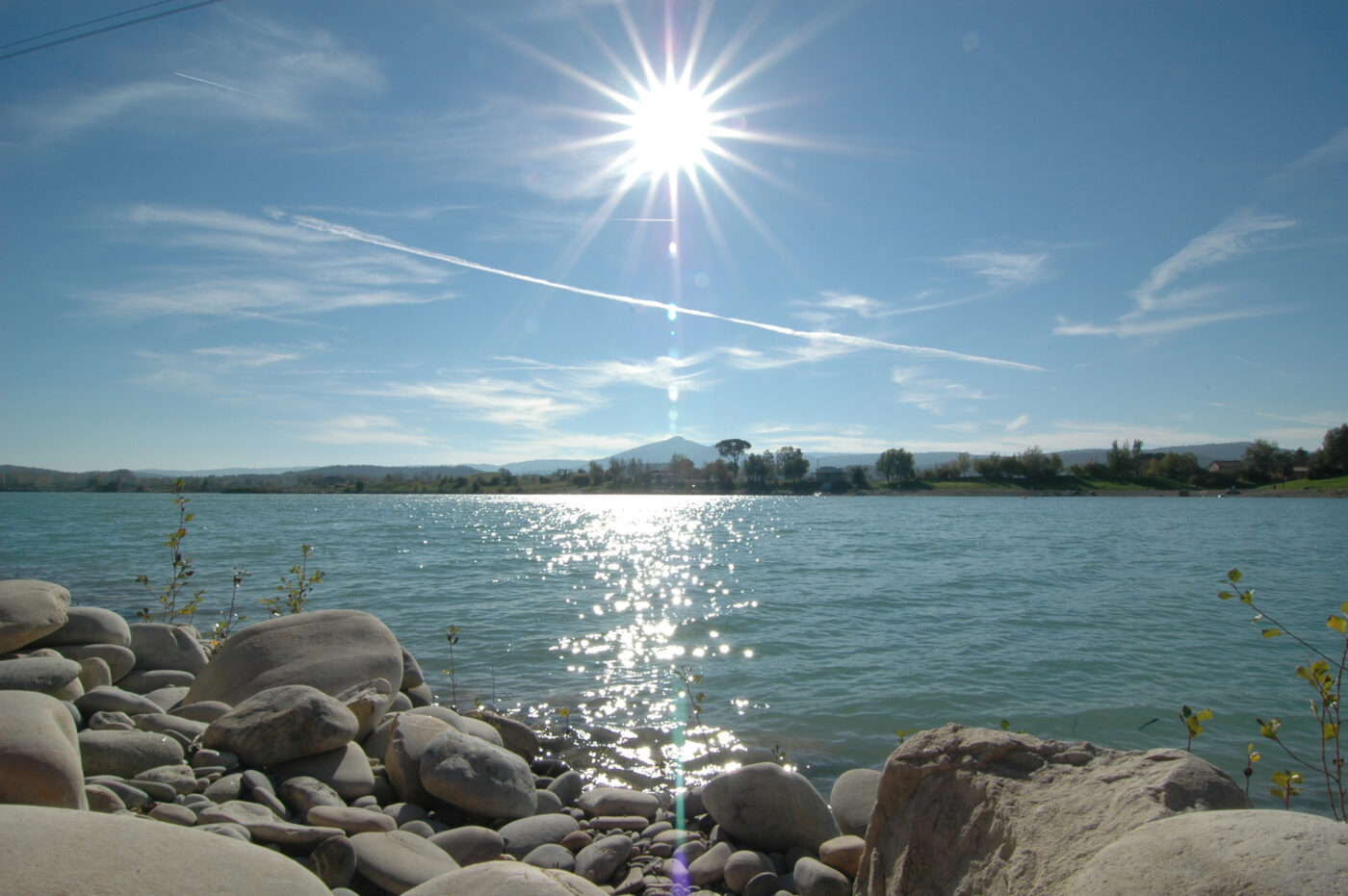
En savoir plus sur la production de granulats
Concilier l’approvisionnement durable des territoires en matériaux minéraux et la préservation de l’environnement constitue l’ambition première des entreprises de l’UNPG. Au-delà du cadre règlementaire très exigeant, la profession relève les défis environnementaux en déployant une démarche de progrès continu fondée sur l’échange de bonnes pratiques et la collaboration avec les parties prenantes.
Des engagements de qualité
Les caractéristiques des granulats font l’objet d’une attention particulière de la part des producteurs car les exigences des clients varient selon les usages prévus pour le matériau. Un contrôle rigoureux est opéré, en particulier sur la granularité (distribution dimensionnelle des particules), l’angularité, la qualité des fines…
La mise sur le marché des granulats est soumise à l’obligation réglementaire du marquage CE. Dans ce cadre, le producteur déclare que le granulat satisfait aux exigences des normes européennes.
En complément, un marquage NF certifie la conformité des produits aux exigences complémentaires de la norme française (NF P 18-545) et du référentiel de certification NF-Granulats.La marque NF garantit que les caractéristiques des produits ont été vérifiées et validées par des auditeurs et laboratoires indépendants ; l’acheteur a ainsi l’assurance que les granulats possèdent toutes les qualités permettant de réaliser des ouvrages selon les règles de l’art.
Une activité strictement réglementée
Les carrières de granulats sont réglementées par le Code de l’environnement. Les exploitations des carrières constituent juridiquement des Installations Classées pour la protection de l’environnement (ICPE) et sont donc soumises à cette législation spéciale du code de l’environnement.
Selon cette nomenclature, on peut distinguer plusieurs régimes juridiques. Les procédures de création, les règles de fonctionnement et de leur fermeture diffèrent selon chaque rubrique concernée : les grandes carrières sont soumises à procédure d’autorisation du préfet (rubrique 2510-1 de la nomenclature ICPE). Il s’agit de toutes les carrières, à l’exception des petites visées aux rubriques 2510-5 et 2510-6, seulement soumises à procédure de déclaration au préfet.
Outre les textes concernant la législation des installations classées, une section « Carrières » existe dans le Code de l’environnement (article L 515-1 et suivants) ainsi que des arrêtés ministériels de prescriptions et des circulaires complémentaires.
L’arrêté ministériel du 22 septembre 1994 modifié par l’arrêté du 22 octobre 2018, et relatif aux exploitations de carrières et aux installations de premier traitement des matériaux de carrières, fixe les conditions d’implantation dans l’environnement et de limitation des risques et nuisances des carrières : aménagements, accès, déclaration de début des travaux, défrichage, archéologie, extraction, prévention des pollutions, rejets, poussières, bruit, vibrations, remise en état, remblayage, sécurité… Cet arrêté encadre également les opérations de remise en état à l’issue de l’exploitation. Ses prescriptions concernent aussi les installations de traitement des matériaux.
Les inspecteurs de l’environnement chargées de la police des carrières par le préfet sont des fonctionnaires habilités et assermentés des DREAL, chargées de la police des ICPE, sous l’autorité du préfet pour la police administrative, et celle du procureur de la République pour la constatation des infractions pénales. La mission de police administrative ne s’achève que lorsque l’inspecteur des installations classées a constaté la conformité des travaux prévus pour la cessation d’activité par un procès-verbal de récolement.
Une logistique de proximité
Les granulats présentent la spécificité de pouvoir être produits localement pour être consommés localement et répondent ainsi parfaitement aux attentes liées aux circuits courts.
La proximité des sites d’extraction avec les bassins de consommation est un élément clé de la réduction des impacts liés au transport des granulats. Au-delà de la réduction des flux de transport, le circuit court offre la double opportunité de :
- Fixer les emplois non-délocalisables sur les communes ;
- Maintenir des coûts de transports compétitifs (le transport des granulats double leur prix tous les 30 kms).
Pour assurer la production de matériaux dont la société a besoin, les professionnels de la filière sensibilisent les pouvoirs publics à l’importance de positionner les sites d’extraction au plus près des pôles de consommation. Aussi l’exploitation de ces sites fait l’objet d’un dialogue constructif avec les représentants du territoire et les riverains pour une politique de transport locale vertueuse : définition de trajets et respect des horaires, formation et sensibilisation des chauffeurs, mesures pour limiter les poussières, …
Impact environnemental de l’extraction de granulats
L’impact d’une carrière sur l’environnement est beaucoup plus réduit que celui de la plupart des sites industriels. En particulier, elle ne génère aucune émission de produits chimiques. De plus, cette activité est limitée dans le temps.
L’industries des carrières est toutefois consciente de l’existence d’impacts : bruit, poussières inertes, vibrations, transport induit par les livraisons, incidences sur la faune, la flore et sur le paysage. Elle entend les maitriser le mieux possible, et à cette fin, recherche toujours les outils et process les plus appropriés.
Depuis 1993, la profession s’est volontairement dotée de méthodes, compétences et moyens spécifiques pour maitriser les impacts environnementaux, au travers de dispositifs ayant évolué au fil du temps pour devenir, en 2017, Cap environnement et Label RSE, tous deux portés par l’association UNICEM entreprises engagées.
Par ailleurs, une carrière en cours d’exploitation peut abriter des espèces, parfois rares, qui trouvent là un milieu favorable. Des inventaires écologiques ont permis d’identifier cette richesse et de nombreuses études ont été menées et publiées par l’UNPG. Sur les carrières réaménagées, on constate également la présence de milieux et d’espères animales et végétales intéressants. Le réaménagement d’une carrière se fait au fur et à mesure que l’exploitation progresse, L’objectif de remise en état par remblayage de la zone d’extraction vise à rétablir une continuité entre les reliefs alentour et la zone d’extraction. En milieu immergé, la restitution d’un aspect naturel est privilégié avec des profils de berges variés et adaptés aux caractéristiques du site afin de favoriser une diversité écologique.